Microsoft Moab - Ball Balancing Robot
Microsoft Bonsai partnered with us to design hardware that would showcase the power of their AI software in an effort to onboard engineers to their platform. The point of the system is to provide the playground where engineers tackling various problems can learn how to use the tooling and simulation models. Once they understand the concepts, they can apply it to their own novel use case. Creating a ball balancing robot that uses Bonsai creates a unique challenge that allows for a solution that incorporates computer vision, Artificial Intelligence and hardware.
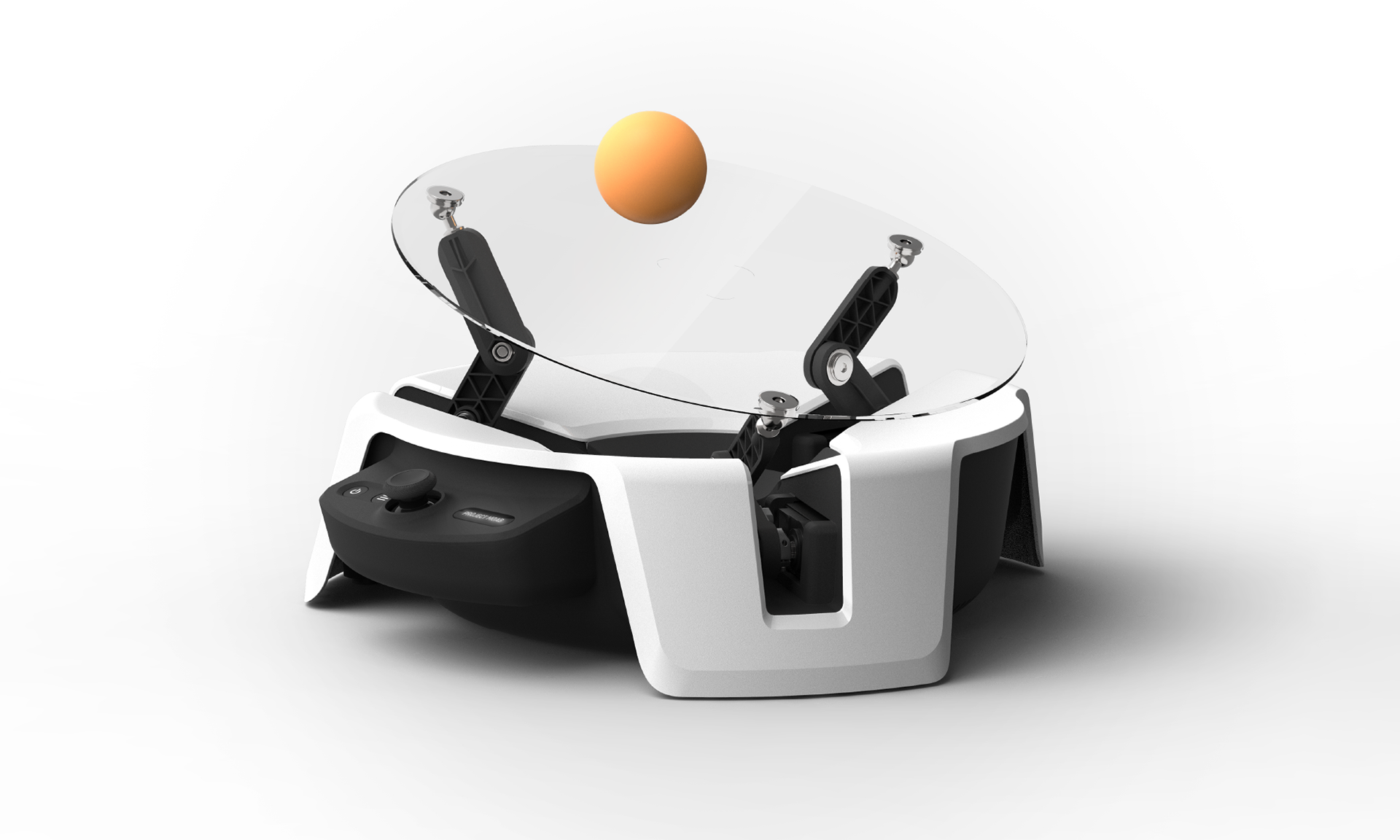
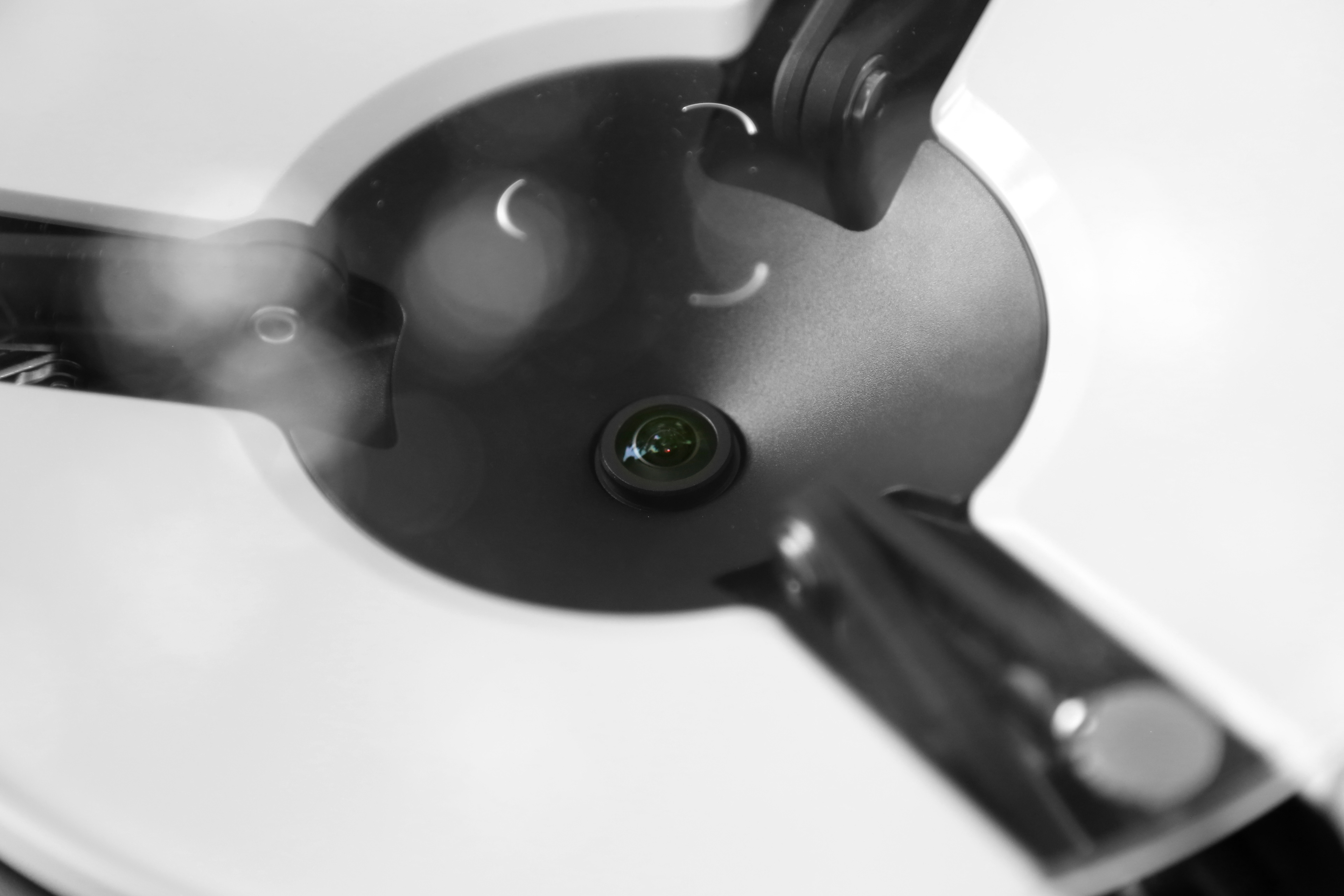
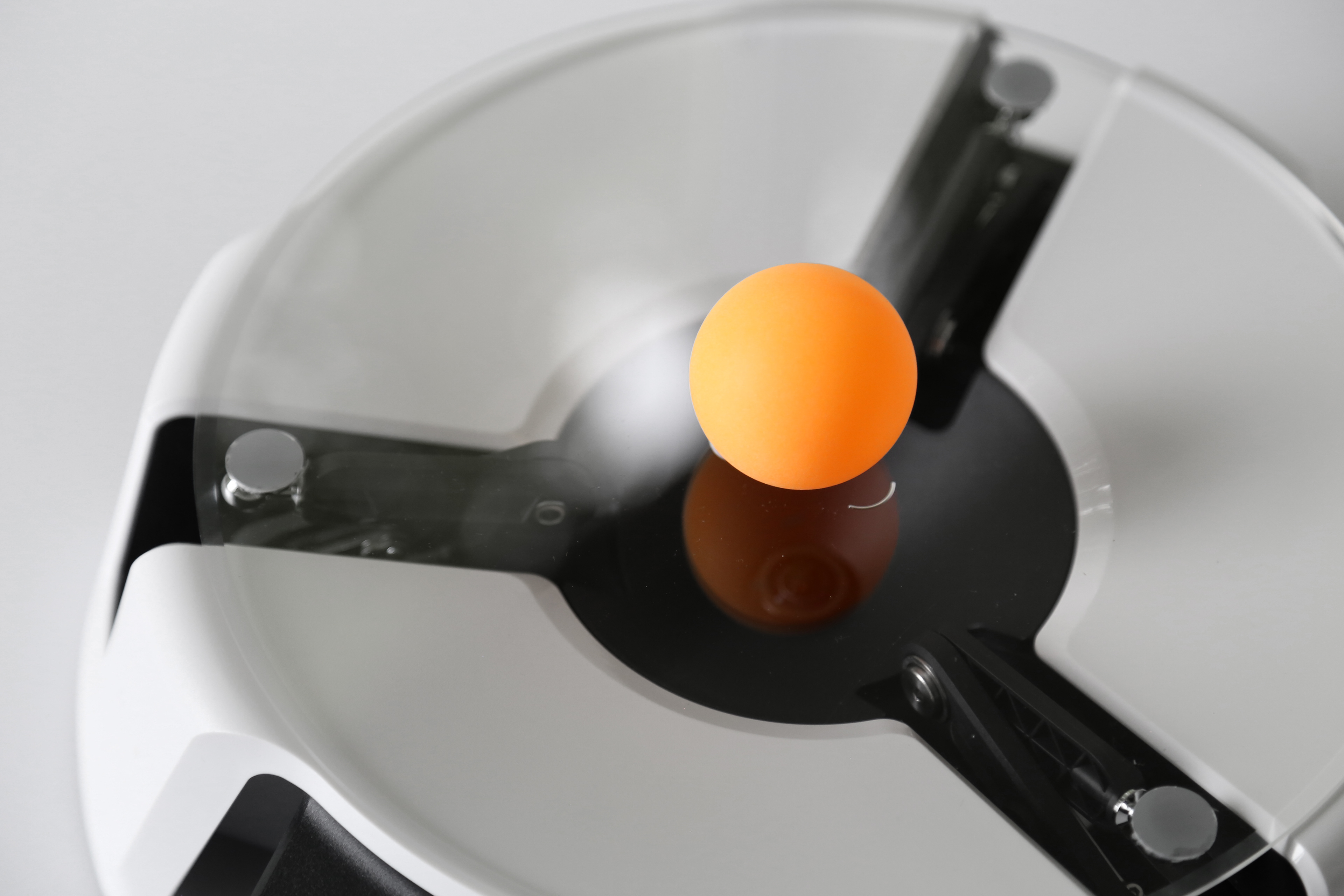
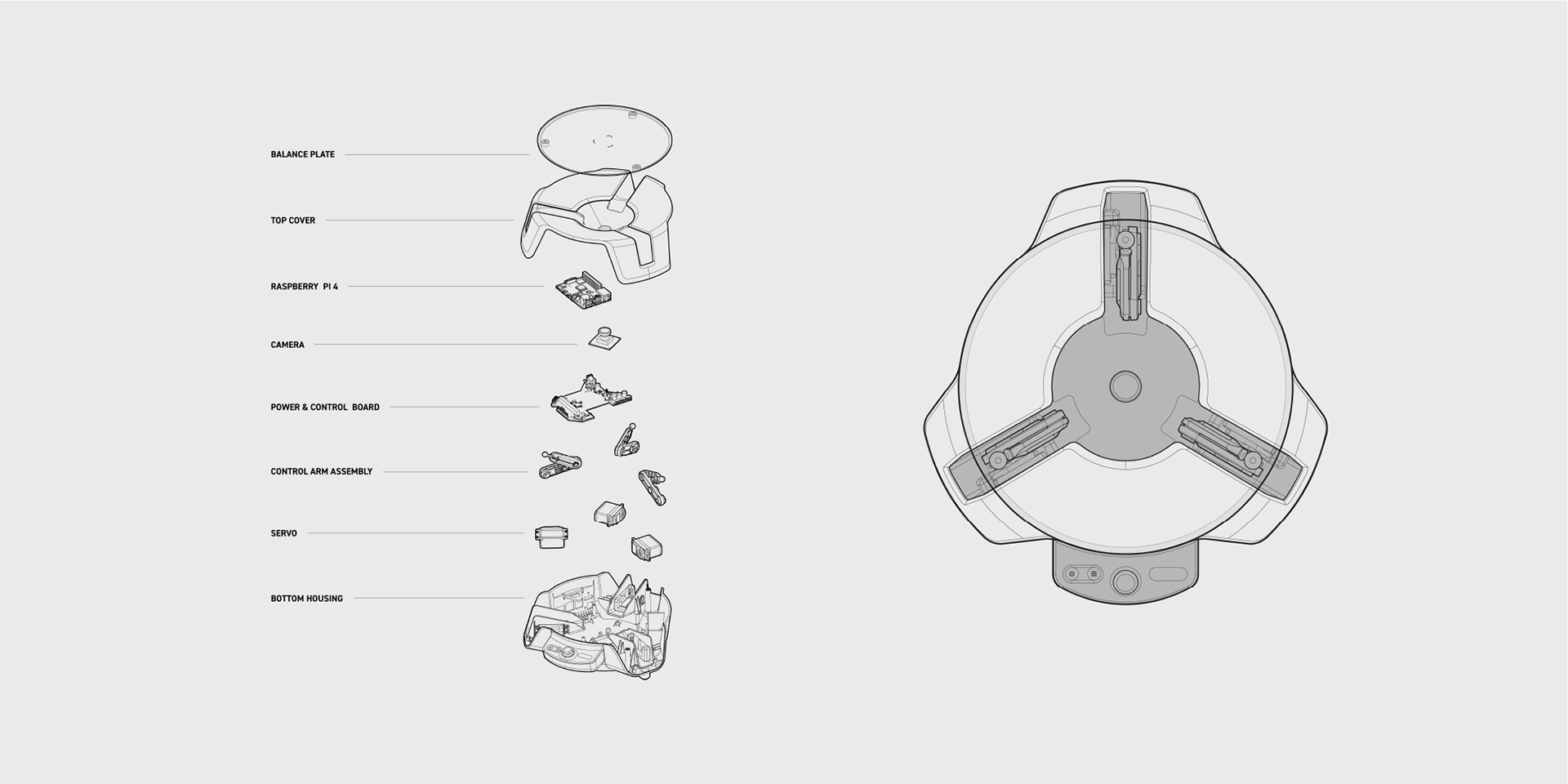
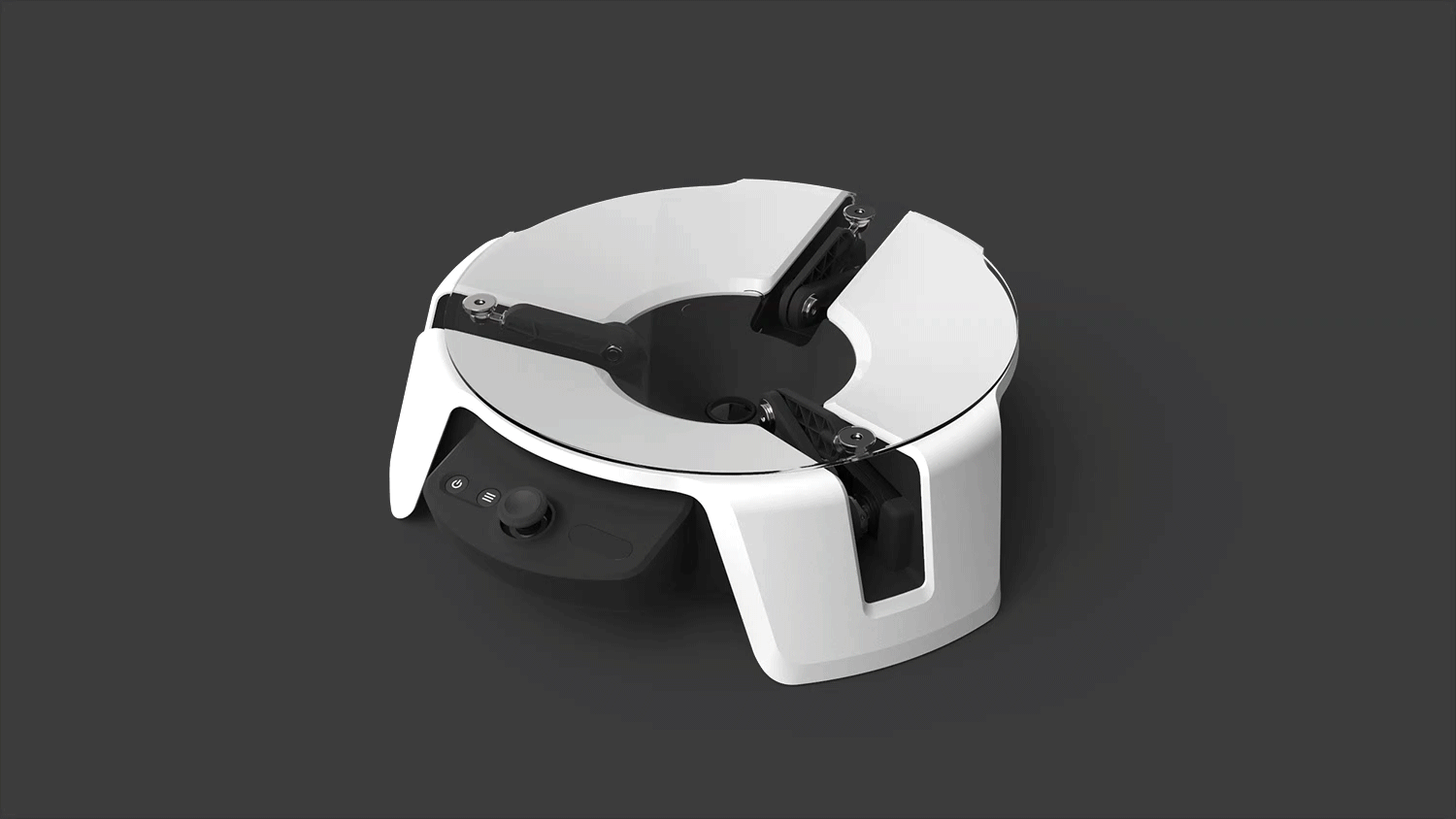
END-TO-END PRODUCT DESIGN & DEVELOPMENT
Creating Moab was a holistic, interdisciplinary effort. From programming the software to designing the hardware, collaboration guided our process. At every stage, the experience of the end-user was considered, while keeping in mind business, design, and manufacturing constraints.
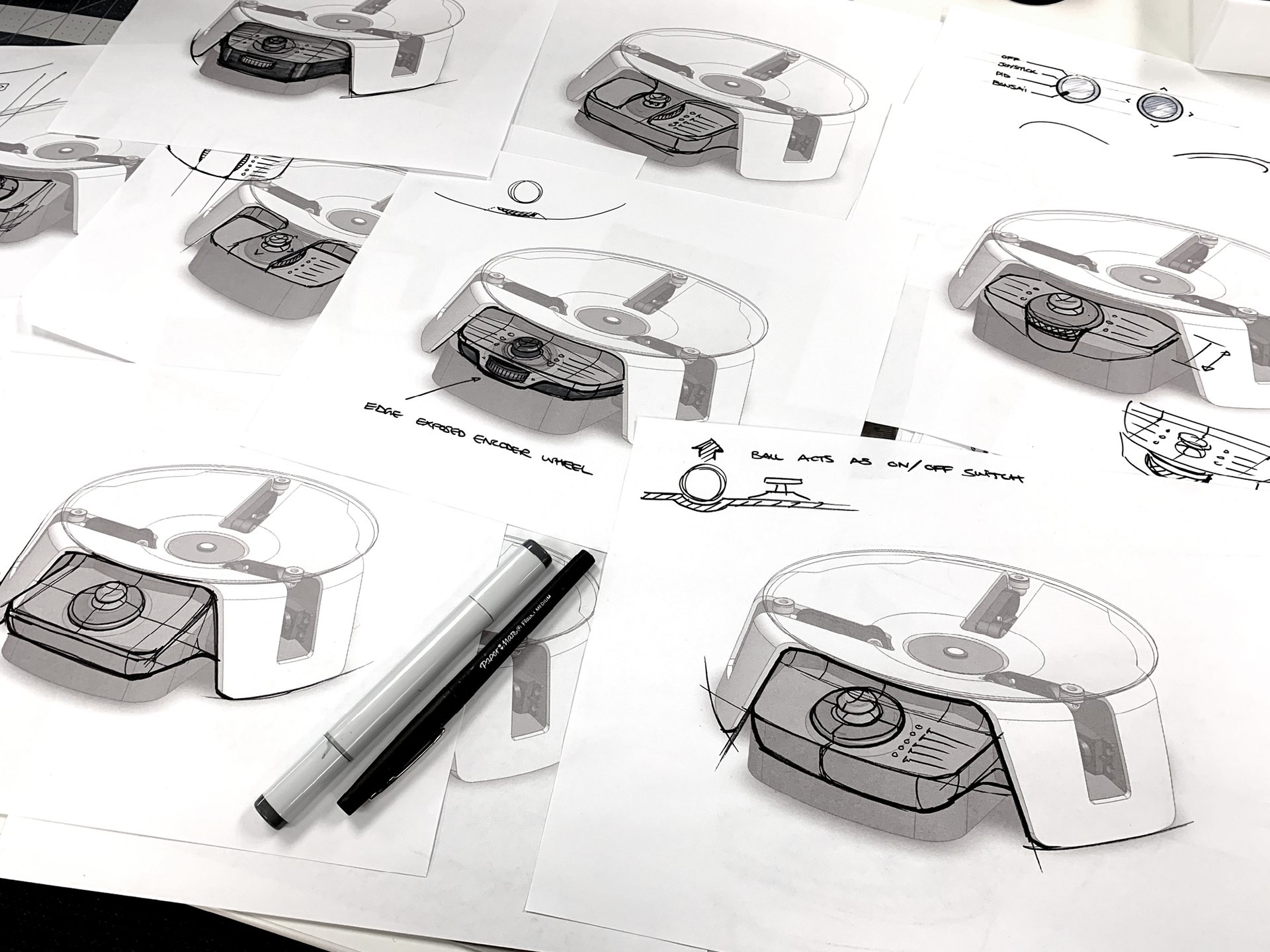
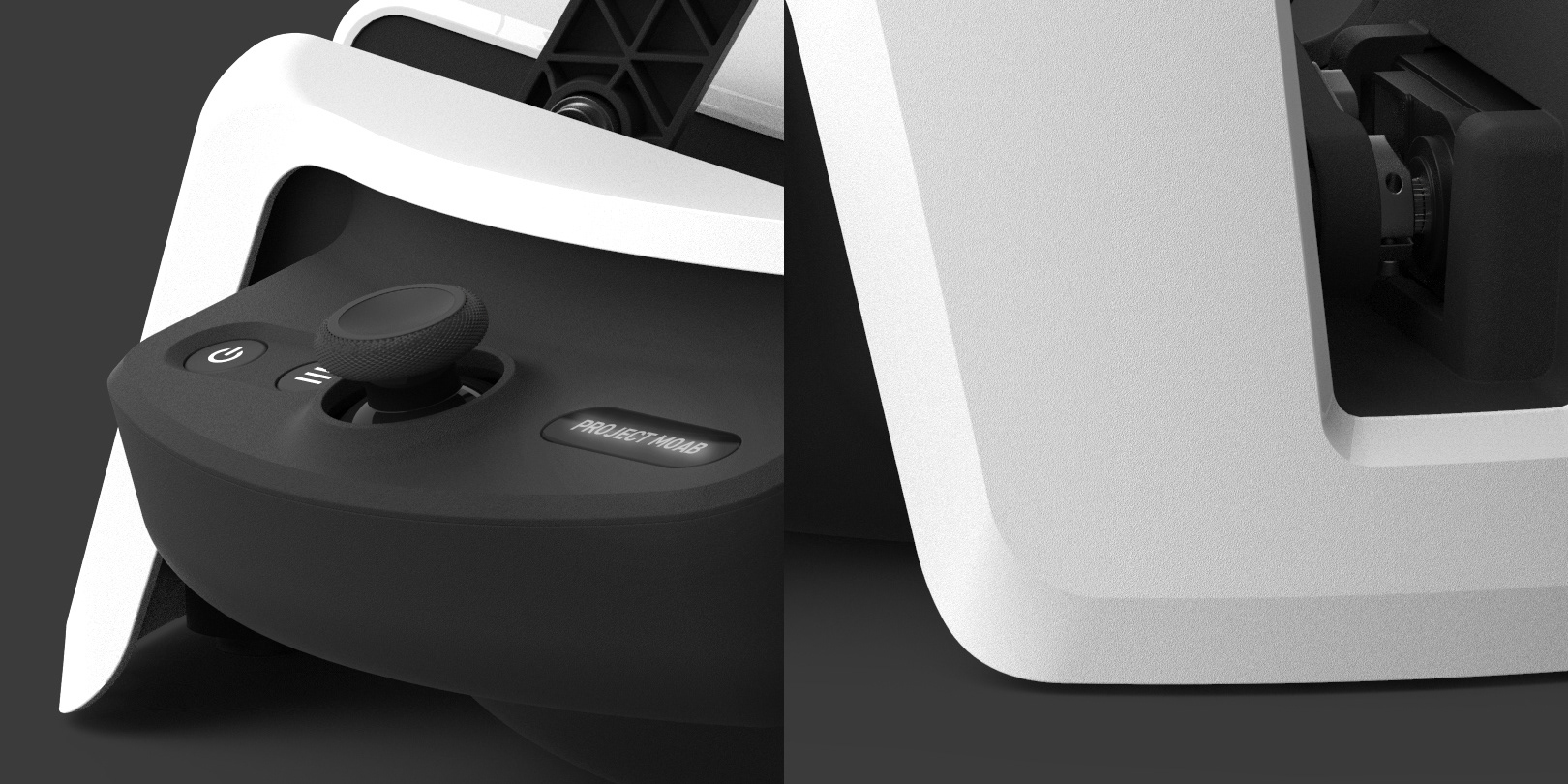
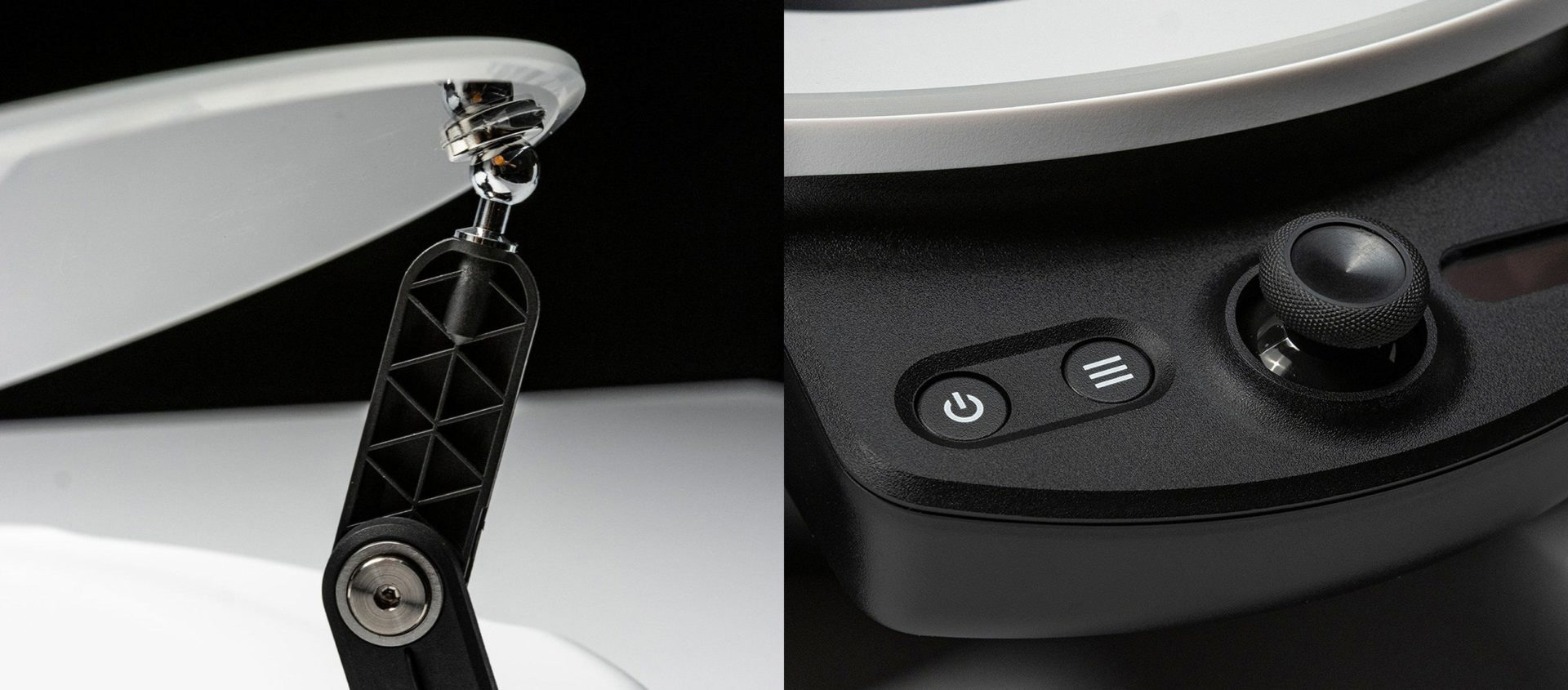
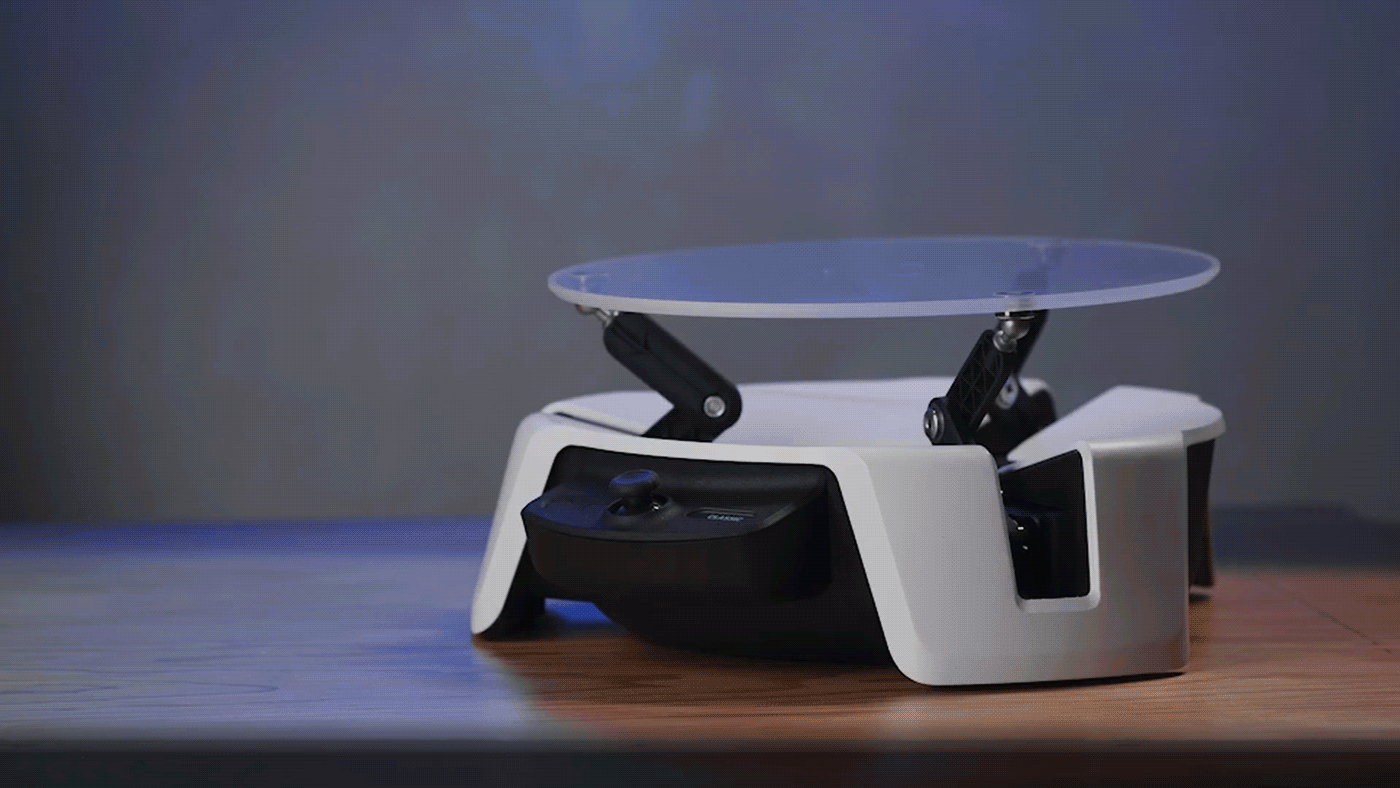
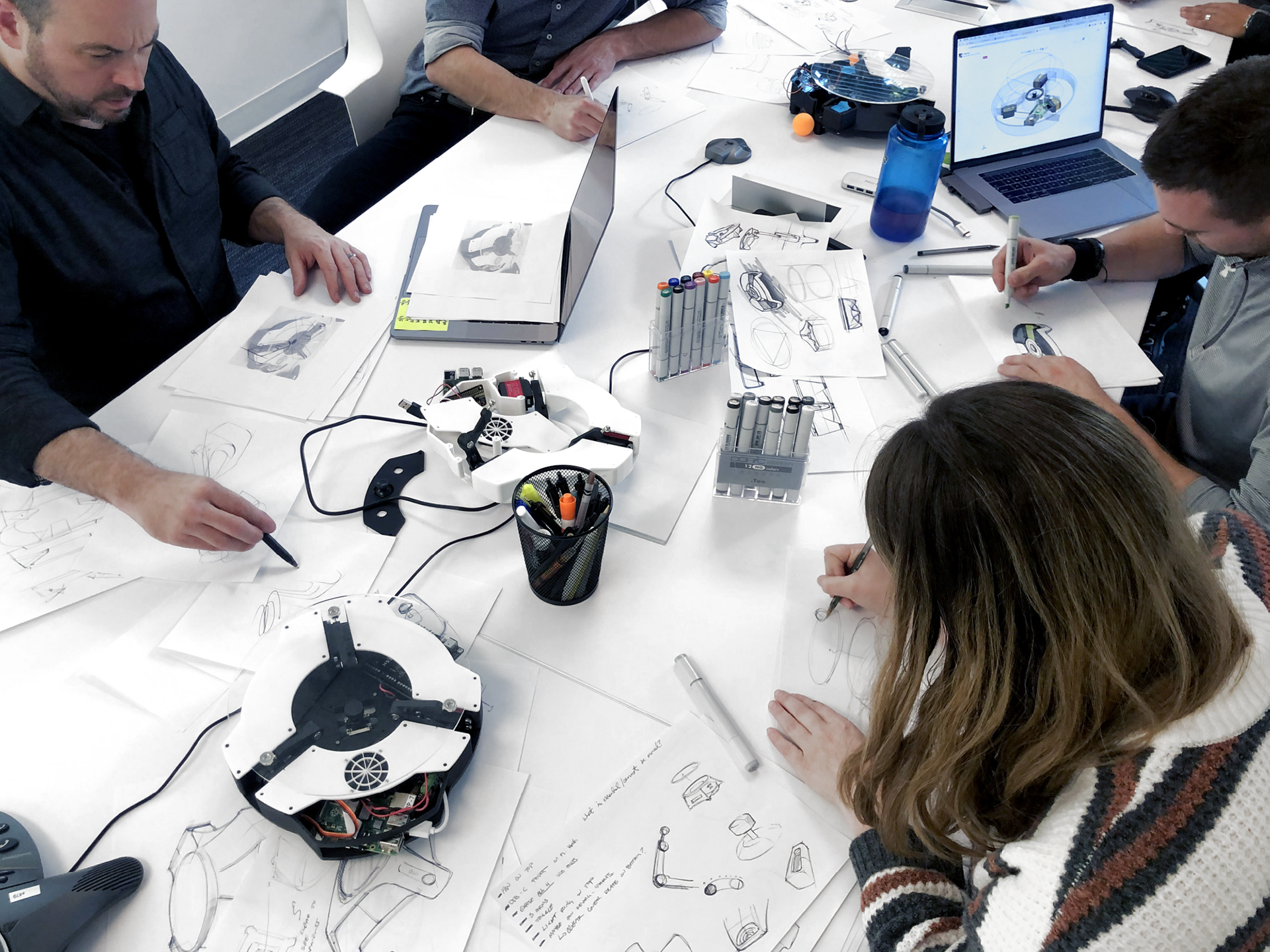
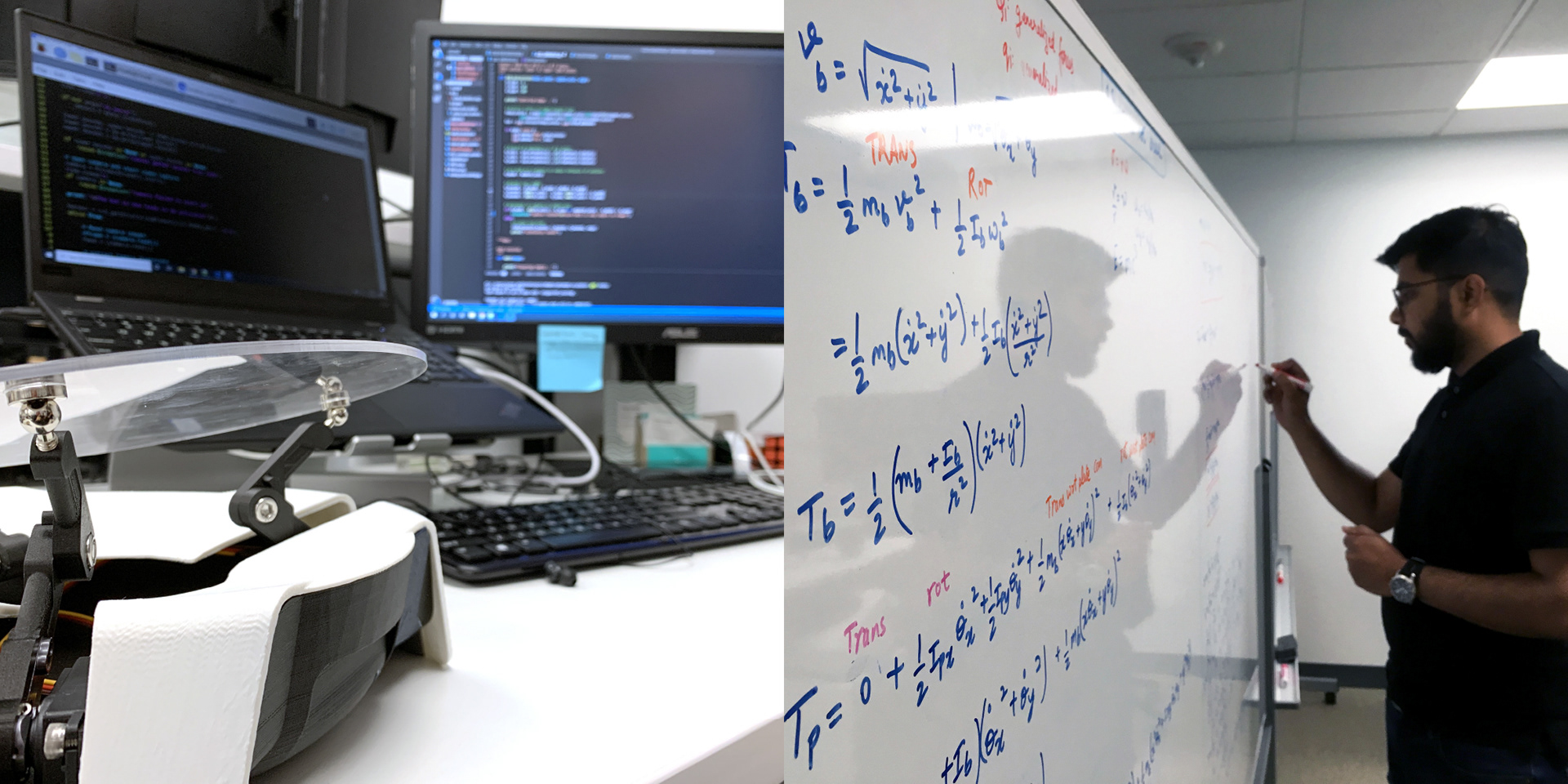
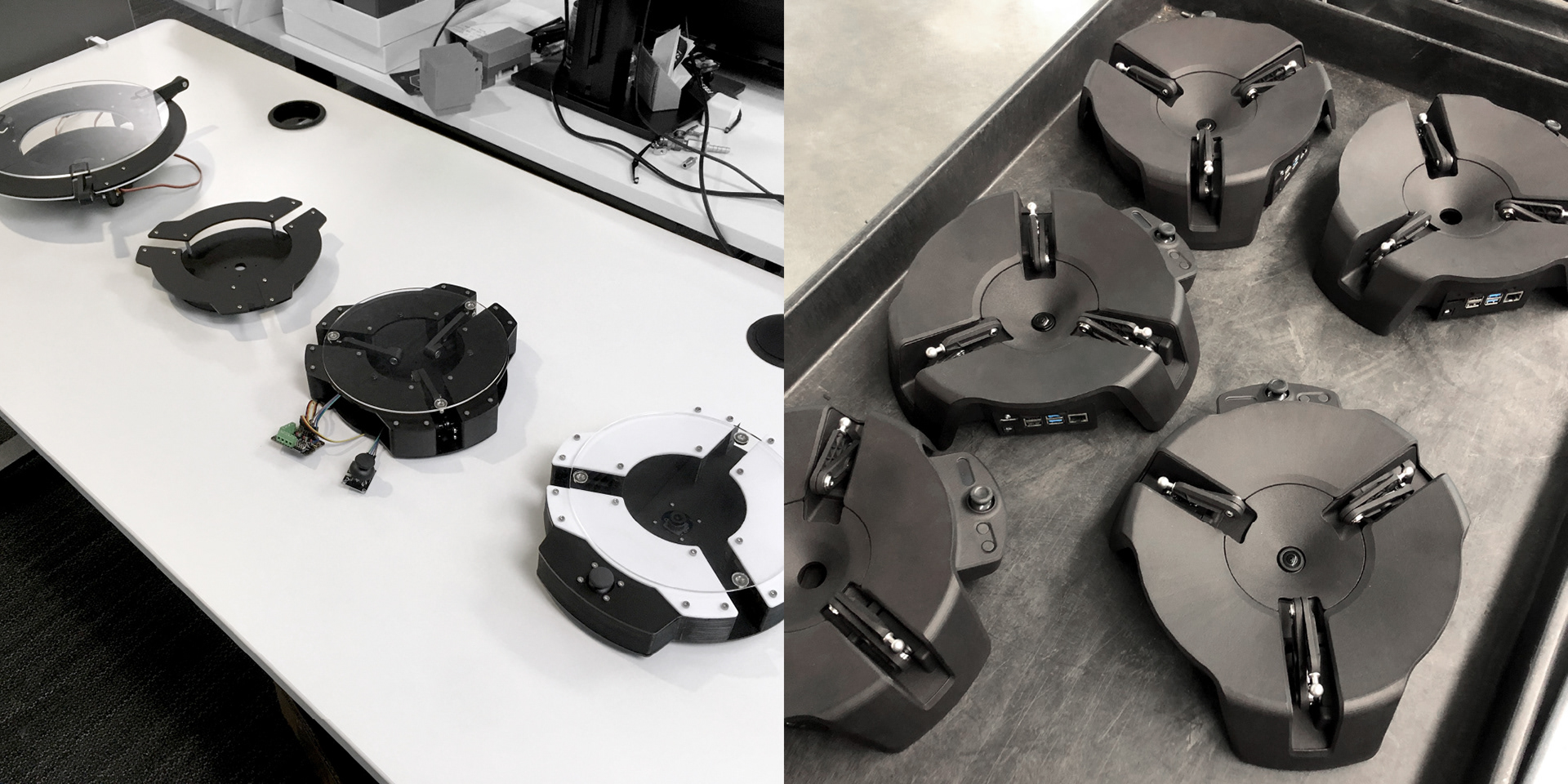
CREATING A CUSTOM PCB
Printed circuit boards, or PCBs, often come as off-the-shelf solutions. For Moab, this wasn’t possible given the unique requirements and specifications of the project. Our engineers and industrial designers collaborated to create a custom PCB with all of the extensive inputs necessary while integrating seamlessly into the unique size and shape of the robot. A custom PCB also allowed us to meet unique requirements and specifications while maintaining reasonable cost, with the eventual goal of creating hundreds of Moab units.
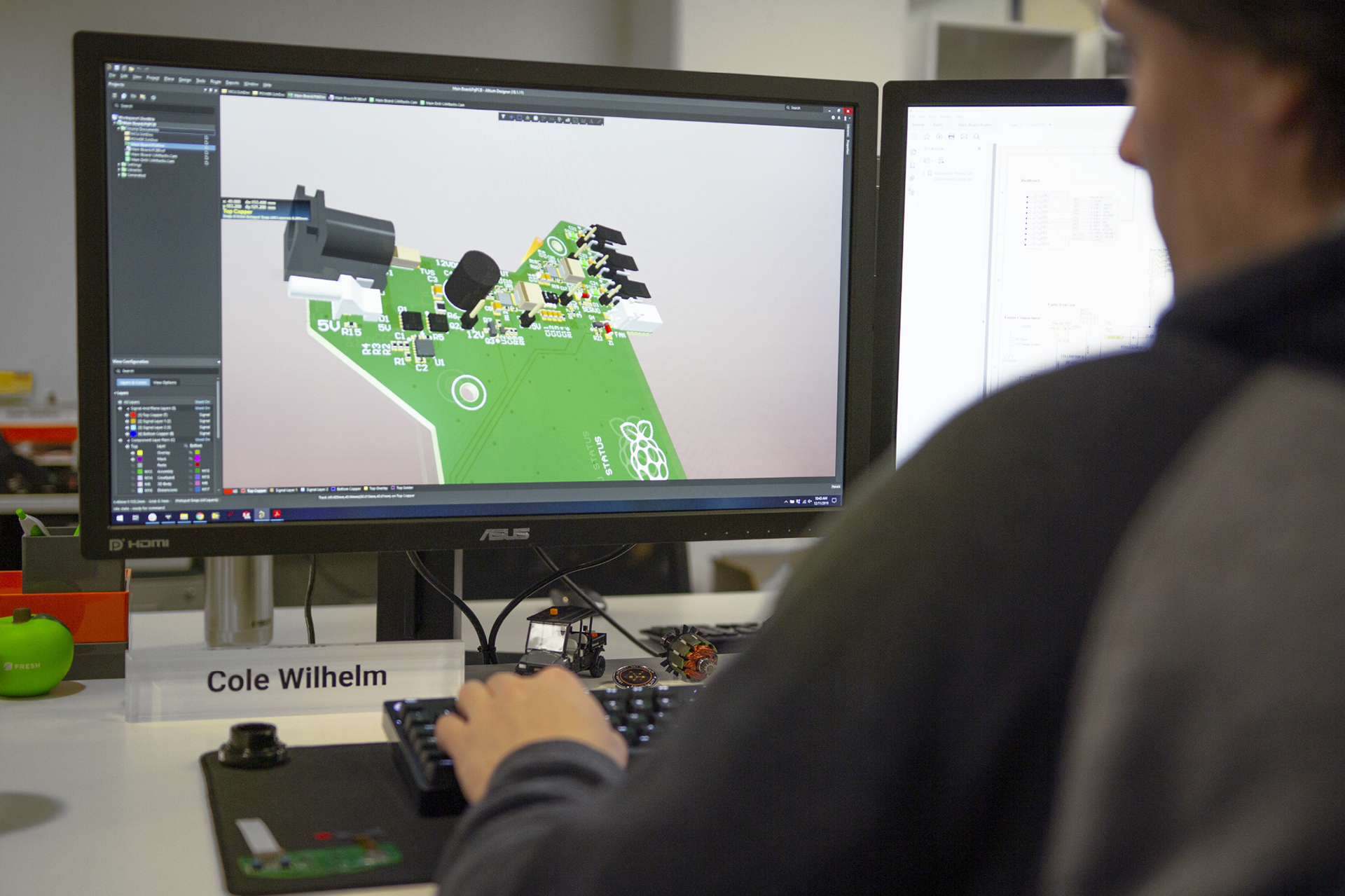
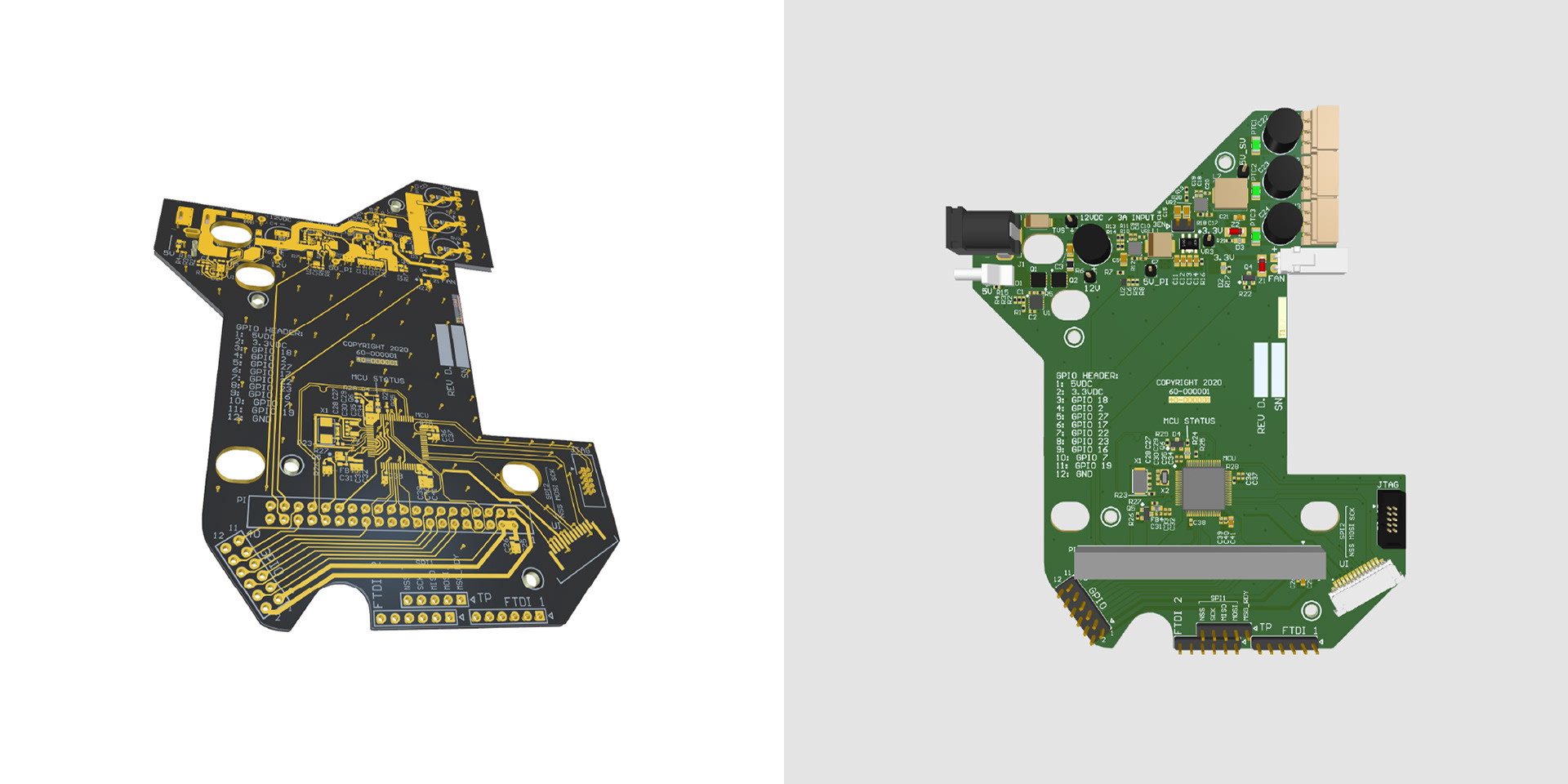
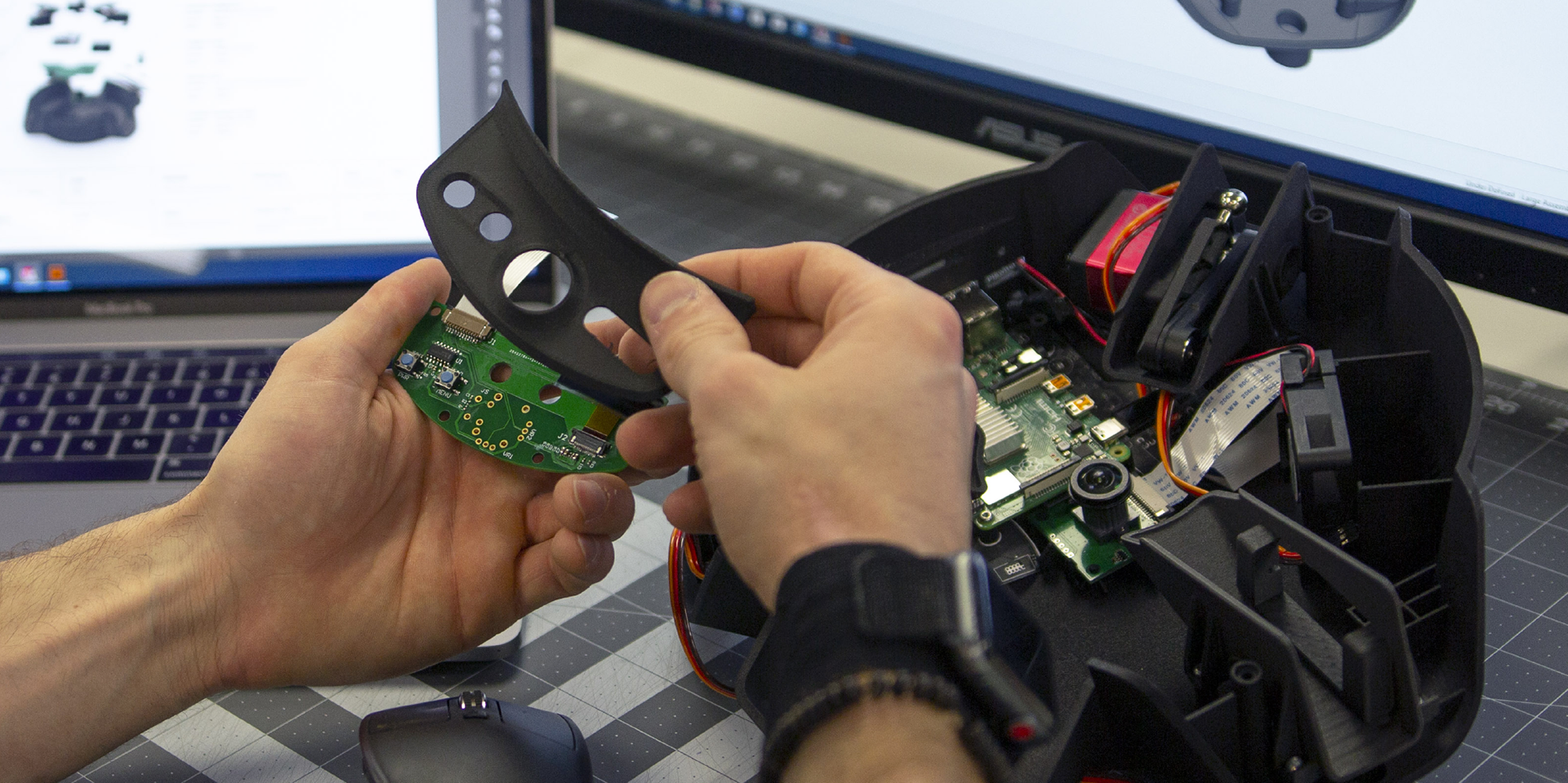
SOFTWARE DESIGN: A PROTOTYPE-FIRST METHODOLOGY
Moab’s success is determined by how well it learns to balance the ball over time. Creating a Moab prototype allowed the software team to write code and test components, helping to push the design forward. Using a prototype-first methodology, we translated abstract ideas and concepts into a testable physical product, where software development efforts supported the ultimate hardware experience.
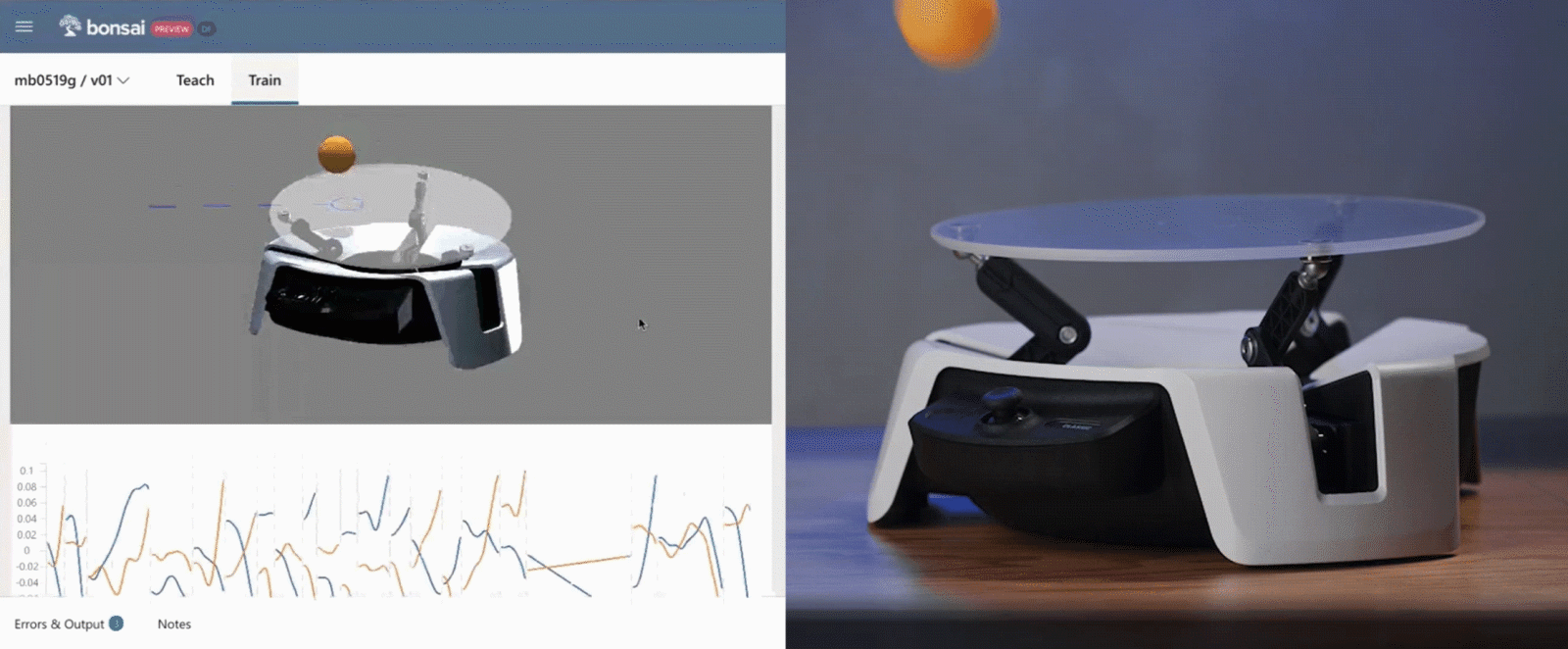
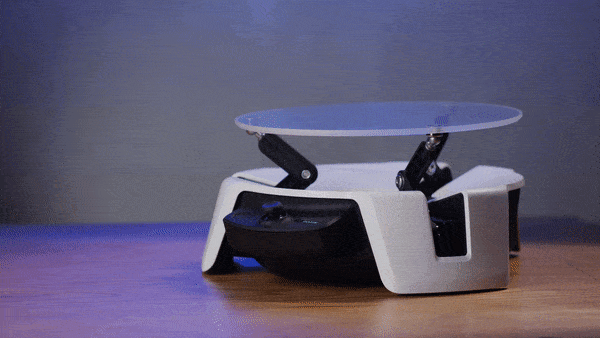
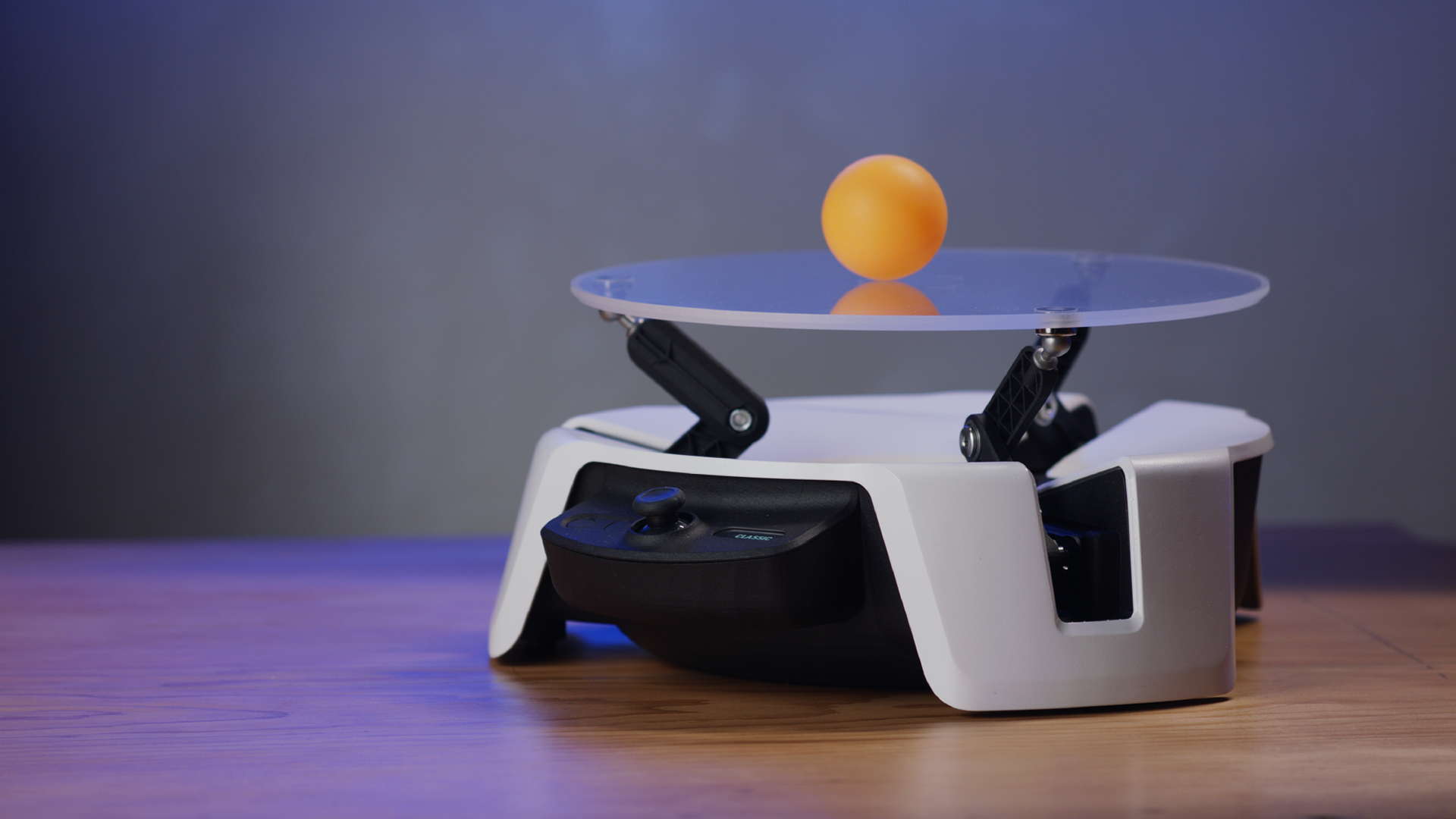
A MANUFACTURING COLLABORATION FROM ACROSS THE WORLD
Working with an experienced overseas manufacturer streamlined our process. We initially used the process of injection molding, shooting Moab’s metal mold with liquid hot plastic that cooled, forming the part. This allowed our team to see through the plastic to test fitting and alignment, confirming that the specifications were exact before getting them into the correct color, material, and finish.
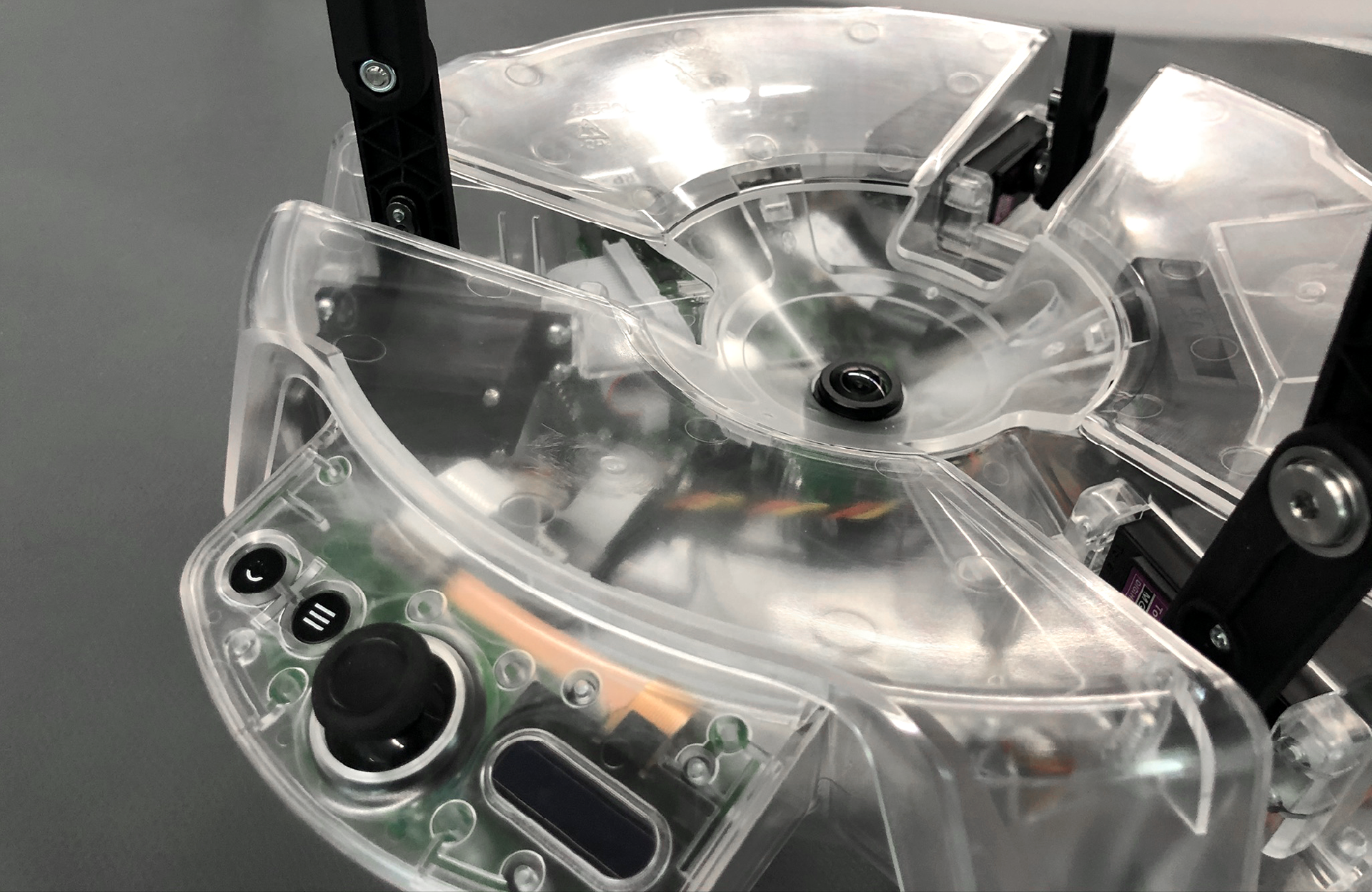
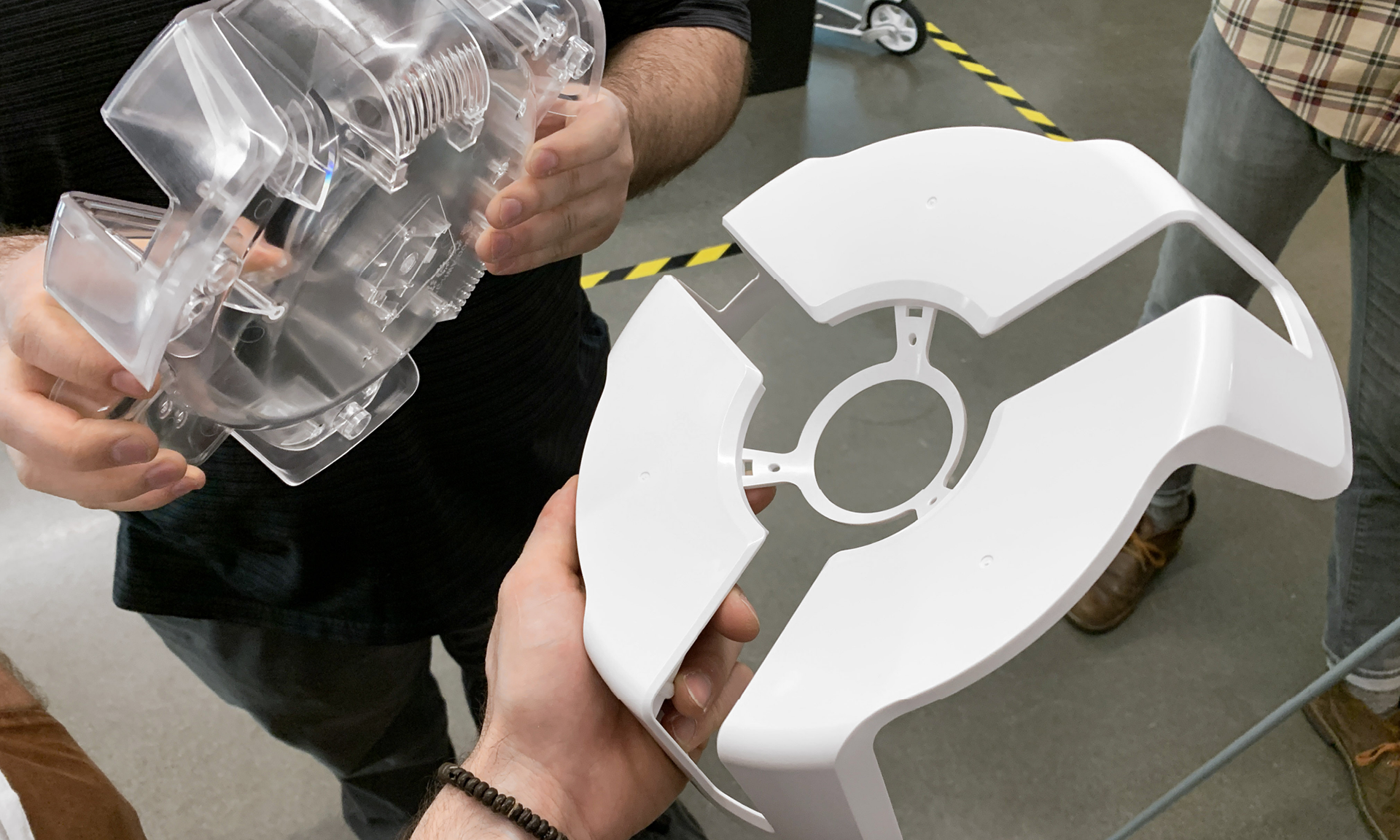
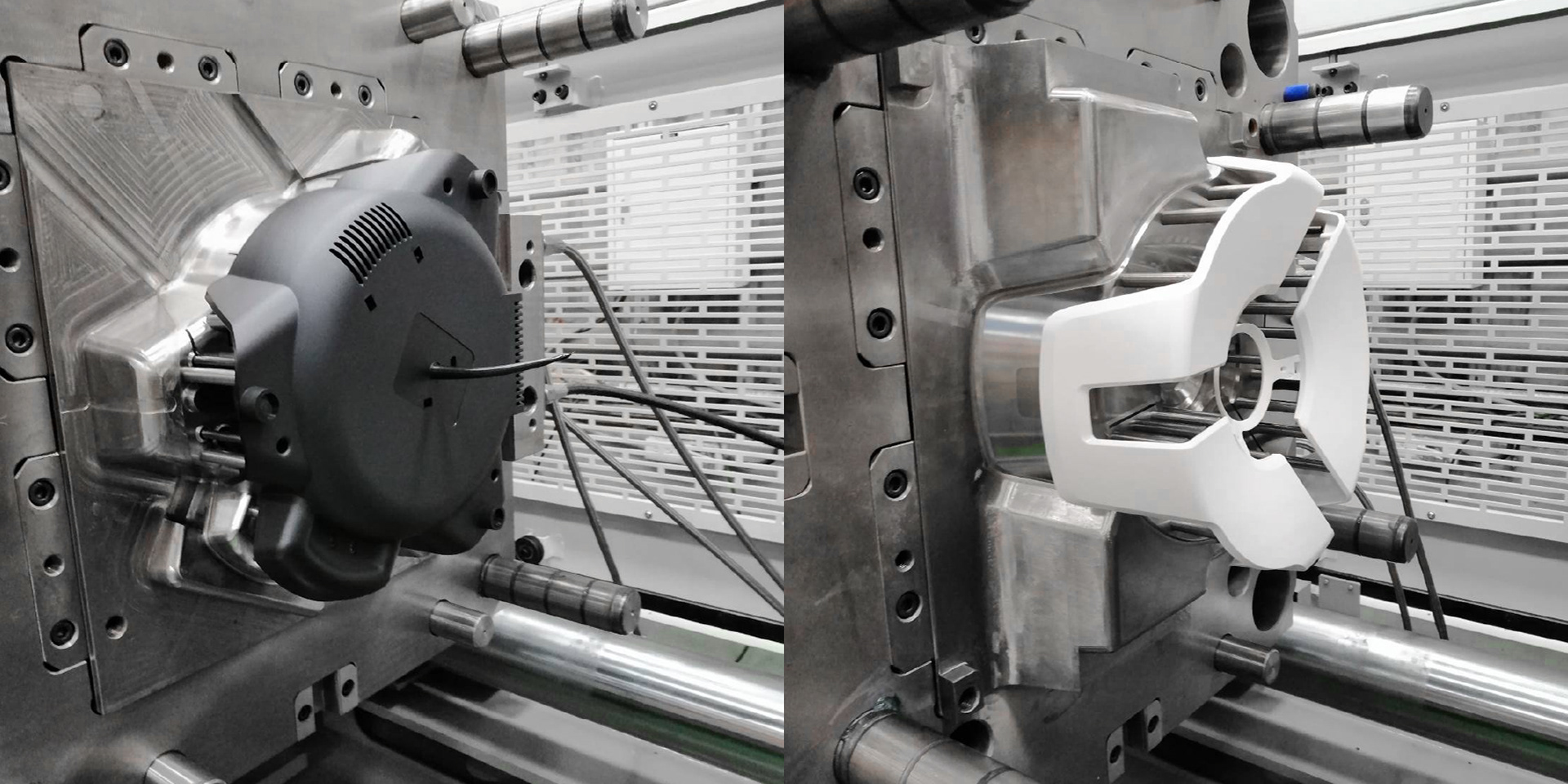
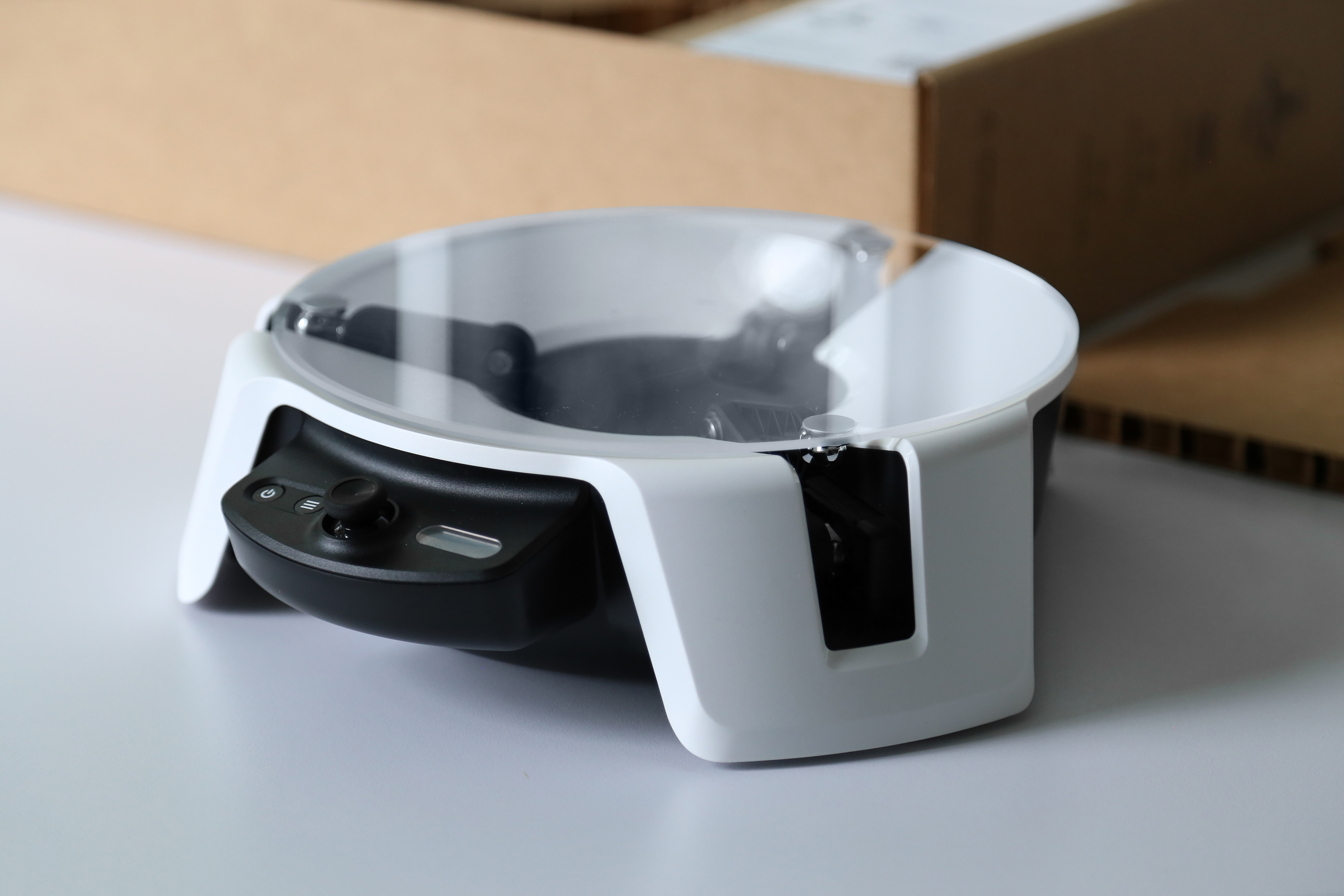
CONSIDERING CX: CREATING THE FULL PACKAGE
The packaging is one of the first experiences a customer has with a product. We wanted the simplicity, clarity, and sophistication of Moab to reflect what customers first see when it arrives.
We opted for a minimalist packaging concept, from the words printed on the box to how it unfolds. The end result is a product that, from packaging to performance, helps engineers learn to develop intelligent control systems and communicates the value of human-centered design thinking.
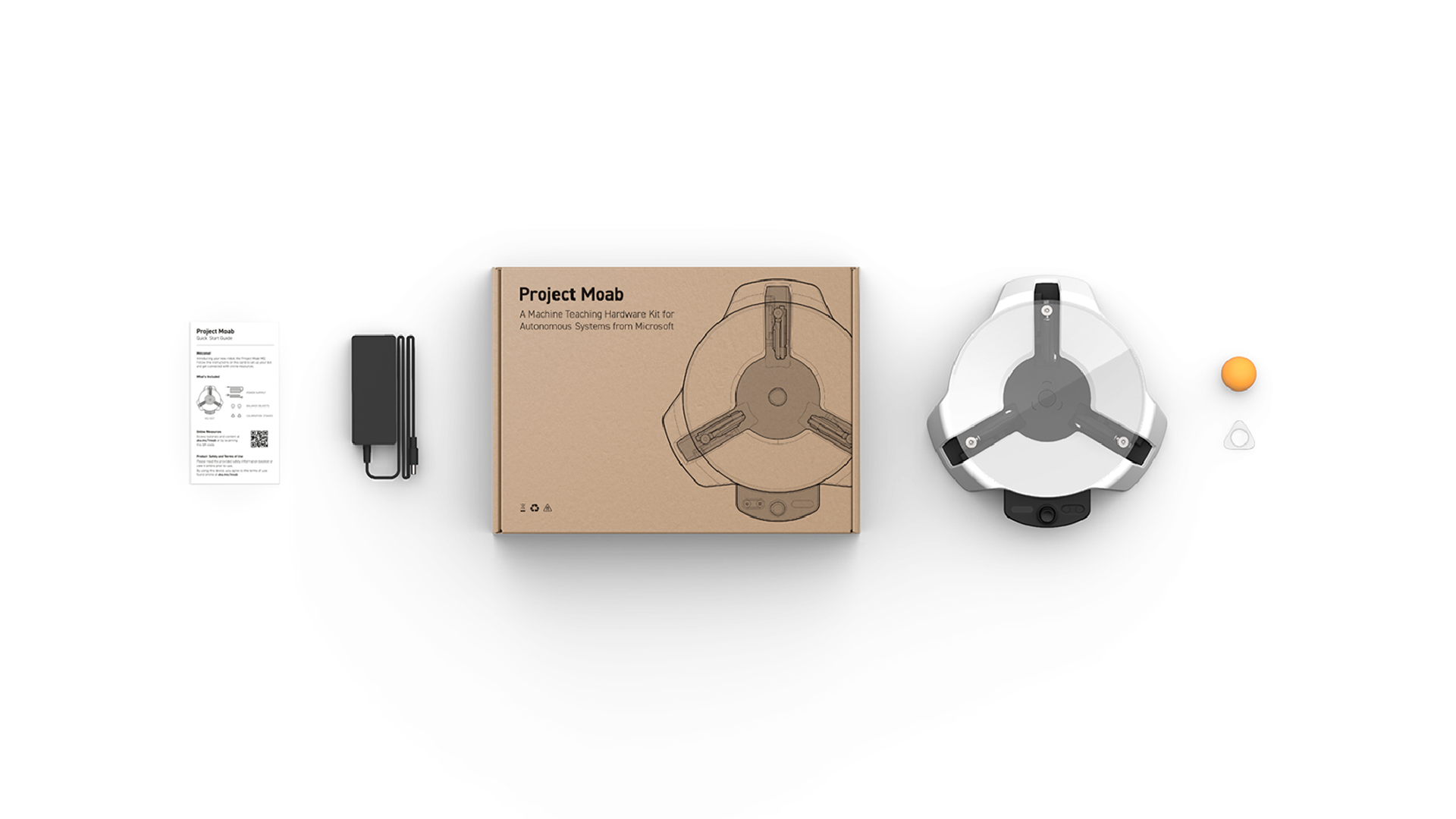
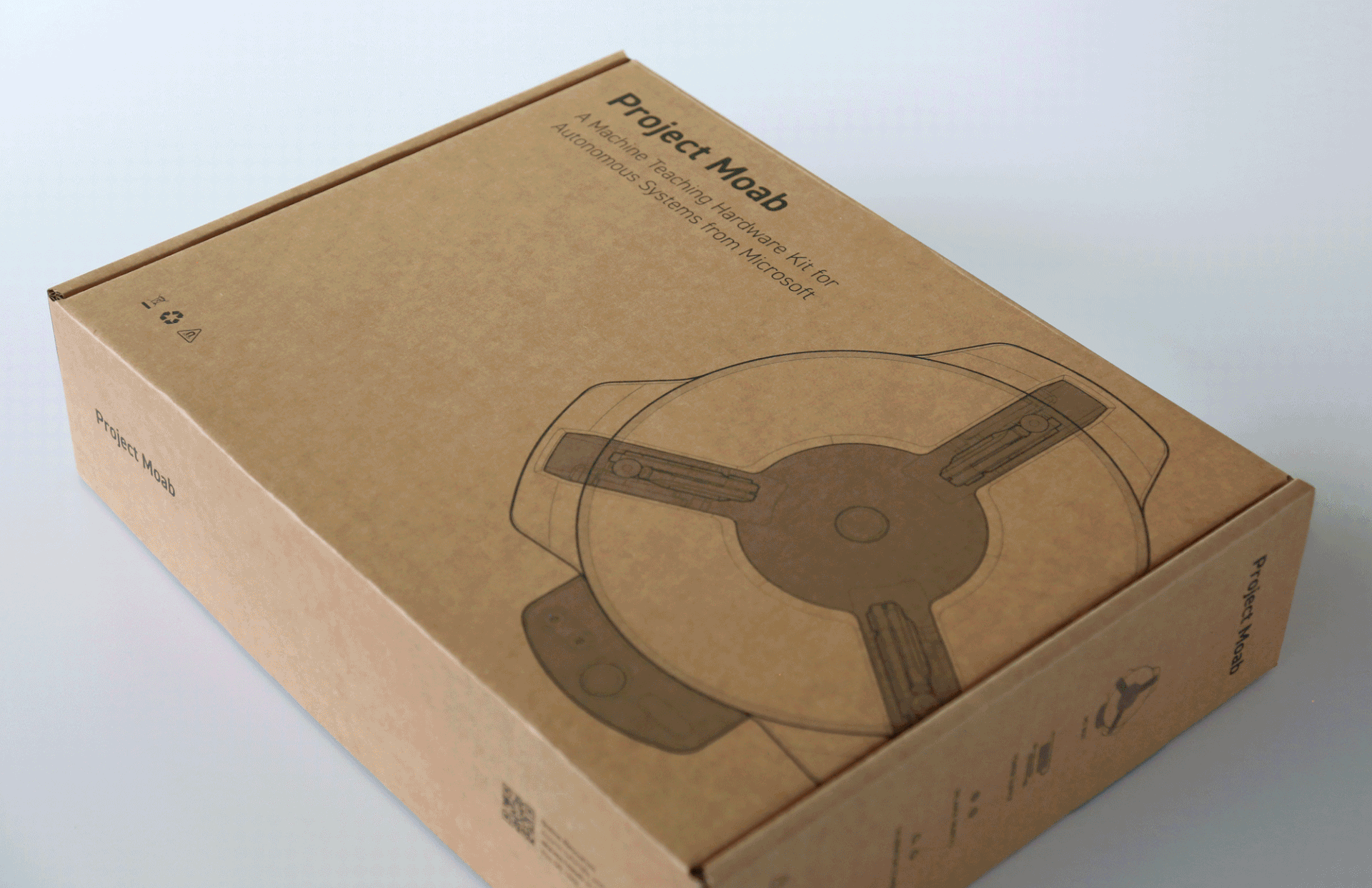
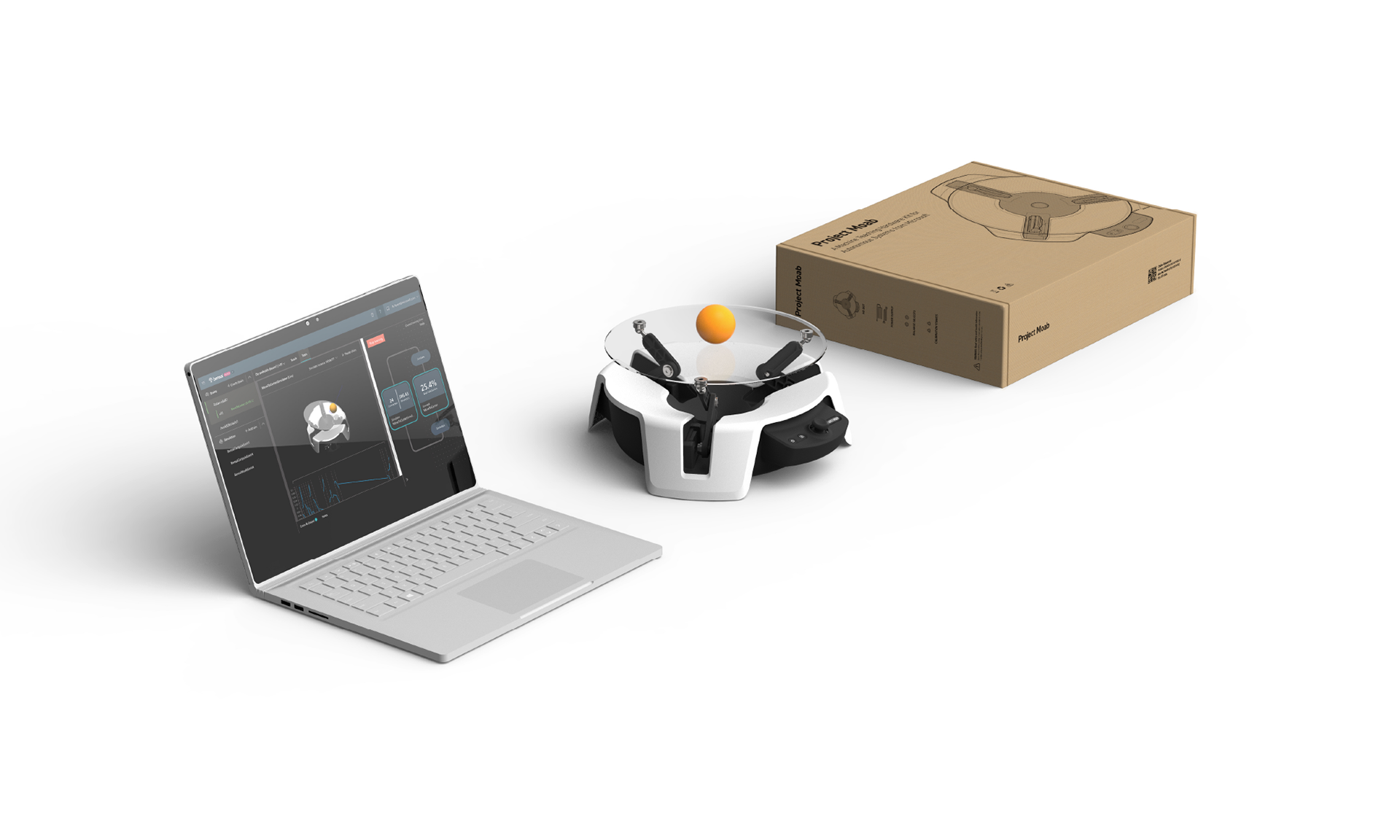
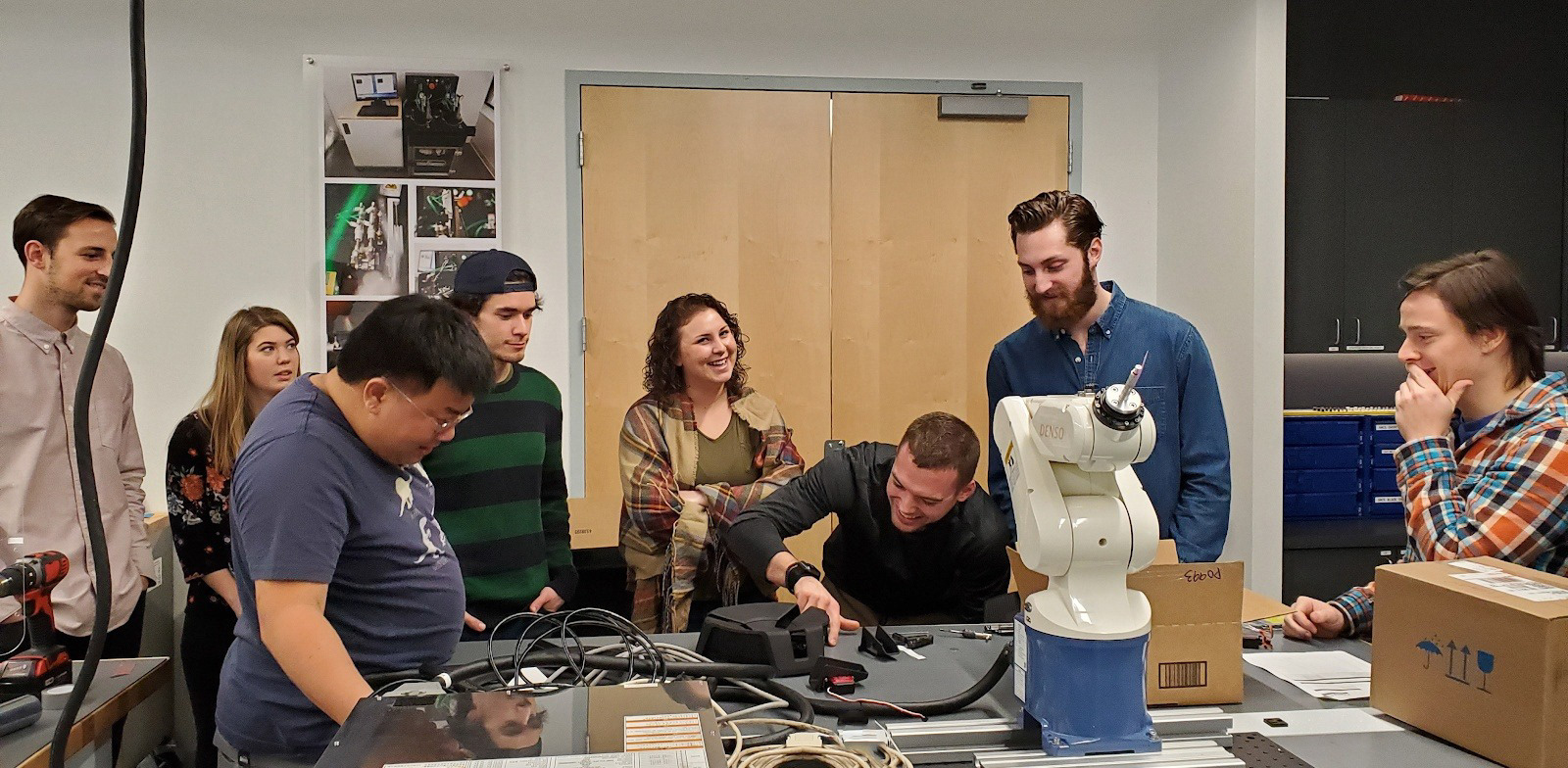